Brushless Motors BXII Series
BXM230M-GFS+GFS2G10+BXSD30-A2
การจำแนกประเภทผลิตภัณฑ์ | ชื่อผลิตภัณฑ์ | รายการราคา | วันที่จัดส่ง |
---|---|---|---|
Motor | BXM230M-GFS | THB 16,032 | 17 Working Days |
Gearhead | GFS2G10 | THB 3,488 | 8 Working Days |
Control Circuit | BXSD30-A2 | THB 11,585 | 17 Working Days |
When connecting to a driver, use a connection cable or flexible connection cable.
รวม
- Motor: None
Gearhead: Mounting Screws, Parallel Key
Control Circuit: Connector for CN1, Connector for CN5, Connector for CN7, Mounting Bracket for Control Circuit (with Screws)
ข้อมูลเฉพาะ
ลักษณะเฉพาะ
ขนาด
ดาวน์โหลดข้อมูล
ข้อมูลเฉพาะอื่น ๆ
Common Specifications
Item | Speed Control Mode | Position Control Mode |
---|---|---|
Input Signals | Photocoupler Input Input Resistance: 6.6 kΩ Operated by Internal Power Supply: 5 VDC Connectable External Power Supply: 24 VDC −15∼+20% 100 mA min. Sink input/source input Supported through external wiring |
|
Arbitrary signal assignment to IN0∼IN8 input (9 points) is possible. []: Initial setting [FWD], [RVS], [M0], [M1], [M2], [M3], [FREE], [STOP], [ALM-RST], TH, TL, S-ON, HMI, [Not Used] |
Arbitrary signal assignment to IN0∼IN8 input (9 points) is possible. [ ]: Initial setting [START], [M0], [M1], [M2], [M3], [FREE], [STOP], [ALM-RST], [HOME], [HOMES], TH, SSTART, MS0, MS1, MS2, MS3, MS4, MS5, FWD, RVS, +JOG, -JOG, S-ON, P-PRESET, TL, HMI, Not Used |
|
Output Signals | Photocoupler and Open-Collector Output External Power Supply: 4.5~30 V DC, 100 mA max. Sink Output/Source Output Supported through external wiring |
|
Arbitrary signal assignment to OUT0∼OUT2 output (3 points) is possible. [ ]: Initial setting [ALM], [WNG], [MOVE], END, TLC, VA, ZSG |
Arbitrary signal assignment to OUT0∼OUT2 output (3 points) is possible. [ ]: Initial setting [ALM], WNG, MOVE, [READY], [HOME-P], END, TLC, VA, ZSG |
|
Transistor and Open-Collector Output External Power Supply: 4.5~30 V DC, 20 m max. |
||
ASG, BSG 500 pulses/revolution | ||
Protective Functions | When the following protective functions are activated, the ALM output turns OFF and the motor will stop. The alarm code will be displayed on the operation panel at the same time. Excessive Position Deviation*, The following errors occur: overcurrent, overvoltage, undervoltage, sensor error, main circuit output error, overload, overspeed, and EEPROM error, initial sensor error, prevention of operation at power-on, regeneration resistor overheat, software overtravel*, operation data* |
|
Maximum Extension Distance | Motor and Driver Distance: 30.7 m (when a connection cable (sold separately) is used) | |
Time Rating | Continuous |
- *For position control mode only
General Specifications
Item | Motor | Driver | |
---|---|---|---|
Insulation Resistance | 100 MΩ or more when a 500 VDC megger is applied between the windings and the case after continuous operation under normal ambient temperature and humidity. (Except for the encoder) |
After continuous operation at normal ambient temperature and humidity, the measurement value between the power supply terminal and the protective earth terminal or the power supply terminal and the signal I/O terminal is 100 MΩ min. using a 500 VDC megger. |
|
Dielectric Strength | No abnormality is observed even with an application of 1.5 kVAC at 50 Hz between the coils and the case for 1 minute after continuous operation at normal ambient temperature and humidity. (Except for the encoder) |
After continuous operation at normal ambient temperature and humidity, no abnormality is observed even if 50 Hz, 1.5 kVAC is applied between the power supply terminal and the protective earth terminal, and 50 Hz, 1.5 kVAC is applied between the power supply terminal and the I/O signal terminal for 1 minute. |
|
Temperature Rise | After continuous operation at normal ambient temperature and humidity, the temperature rise of the windings measured by the thermocouple method is less than 50° C, and the measured temperature rise on the case surface is less than 40 °C*1. |
After continuous operation at normal ambient temperature and humidity, the measurement value of the temperature rise of the heat sink is 50 °C max. using the thermocouple method. (60 °C max. when 200 W and 400 W types are installed in contact with each other) |
|
Operating Environment*2 | Ambient Temperature | 0~+50 °C (Non-freezing) | 0~+50 °C (Non-freezing)*2
0~+40 °C for 200 W and 400 W types when mounted close together |
Ambient Humidity | 85 % max. (Non-condensing) | ||
Altitude | Less than 1000 m above sea level | ||
Atmosphere | No corrosive gases or dust Cannot be used in a radioactive area, magnetic field, vacuum, or other special environments. |
||
Vibration | Not subject to continuous vibration or excessive shock In conformance with JIS C 60068-2-6, "Sine-wave vibration test method" Frequency Range: 10~55 Hz, Single Amplitude: 0.15 mm, Sweep Directions: 3 directions (X, Y, Z), Number of Sweeps: 20 |
||
Storage Conditions*3 | Ambient Temperature | -20~+60°C (Non-freezing) | -25~+70°C (Non-freezing) |
Ambient Humidity | 85 % max. (Non-condensing) | ||
Altitude | Less than 3000 m above sea level | ||
Atmosphere | No corrosive gases or dust Should not be exposed to water or oil. Cannot be used in a radioactive area, magnetic field, vacuum, or other special environments. | ||
Thermal Class | UL/CSA Standards: 105 (A), EN Standards: 120 (E) | − | |
Degree of Protection | IP54 (Excluding the installation surface of the round shaft type and connectors) | IP20 |
- *1
- Attach round shaft types to a heat sink (Material: aluminum) of one of the following sizes to maintain a motor case surface temperature of 90 °C max.
30 W Type: 115×115 mm, 5 mm thickness, 60 W Type: 135×135 mm, 5 mm thickness, 120 W Type: 165×165 mm, 5 mm thickness,
200 W Type: 200 × 200 mm, 5 mm thickness 400 W Type: 250 × 250 mm, 6 mm thickness - Characteristics *2
- Install the driver to a location that has the same heat radiation capability as an aluminum metal plate.
Single mounting: 200 x 200 mm, 2 mm thick
Close Mounting 350x350 mm, 2 mm thickness
For 200 W and 400 W types: Load factor is 90% or less when using driver mounting brackets or DIN rail mounting brackets (sold separately). - *3
- The value for storage condition applies to short periods such as the period during transport.
- Do not measure insulation resistance or perform a dielectric strength test the motor and driver are connected.
Speed Control Mode Specifications
Item | Digital setting | Analog Setting |
---|---|---|
Speed Control Range | 2~4000 r/min (Set in 1 r/min increments) | 30~4000 r/min |
Speed Setting Method |
Set using one of the following methods.
|
Set using one of the following methods. Operation Data No. 0:
Internal Speed Potentiometer (SPEED)
Operation Data No. 1:
|
Acceleration/Deceleration Time | 0.000~30.00s (Rated speed, no load) |
0.1~30s (Rated speed, no load) |
Acceleration/Deceleration Time Setting Method |
Set using one of the following methods. (Individual settings)
|
Acceleration time/deceleration time are common to Operation Data No. 0 and No. 1
|
Torque Limiting Setting Range | 0~250% | |
Torque Limiting Setting Methods |
Set using one of the following methods.
|
Set using one of the following methods.
|
Operation Data Setting Number | 16 Points | |
Operation During Motor Standstill | Operations can be selected when the motor is at standstill. ・Motor non-excitation (initial setting) / ・Servo lock stop (motor excitation) |
|
Other Operations | JOG operation, test operation, teaching (Excluding MEXE02 *1) |
- *1
- The support software MEXE02 can be downloaded from the website. When using MEXE02, the communication cable for support software CC05IF-USB (sold separately) is needed.
- *2
- The maximum voltage can be arbitrarily changed with the parameters. Example: 0~5 VDC
Position Control Mode Specifications
Item | Digital Setting | |
---|---|---|
Positioning Operation |
Traveling Amount Setting Range | −8,388,608~+8,388,607step |
Resolution | 0.72˚ (500 steps/revolution) | |
Speed Setting Range | 2~4000 r/min (Set in 1 r/min increments) | |
Operating Mode | Incremental or Absolute | |
Operation Functions | Independent, Linked, Linked 2, Sequential, Direct | |
Acceleration/Deceleration Time | 0.000~30.00s (Rated speed, no load) |
|
Torque Limiting | 0~250% | |
Operation Data Setting Number | 31 Points | |
How to Set Operating Data | Set using one of the following methods.· ・Operation Panel・MEXE02 * ・OPX-2A(sold separately) (Torque limiting alone can be done with external analog settings as well) |
|
Other Operations | Continuous operation, JOG operation, return-to-home operation, test operation, teaching |
- *The support software MEXE02 can be downloaded from the website. When using MEXE02, the communication cable for support software CC05IF-USB (sold separately) is needed.
Torque Limiting Function
The motor's output torque can be limited in speed control mode and position control mode.
Item | Specifications |
---|---|
Torque Limiting Setting Command |
Set 1 method from the following.
The same torque limiting value applies to all operation data. |
Torque Limiting Setting Range*2 |
Assuming that the rated torque of the motor is 100%, torque limiting value can be set in the following ranges.
|
- *1
- The maximum voltage can be arbitrarily changed with the parameters. Example: 0~5 VDC
- *2
- Do not add a load that exceeds the maximum instantaneous torque.
Note
- An error up to a max. of approximately ±10 % (at rated torque and rated speed) may occur between the setting value and generated torque due to the setting speed, power supply voltage and motor cable extension length.
Permissible Radial Load and Permissible Axial Load
Parallel Shaft Gearhead
Motor Product Name | Gear Ratio | Permissible Radial Load | Permissible Axial Load N |
||
---|---|---|---|---|---|
10 mm From the End of the Output Shaft N |
20 mm From the End of the Output Shaft N |
||||
BXM230 | 5 | At 2~3000 r/min | 100 | 150 | 40 |
At 4000 r/min | 90 | 110 | |||
10, 15, 20 | At 2~3000 r/min | 150 | 200 | ||
At 4000 r/min | 130 | 170 | |||
30, 50, 100, 200 | At 2~3000 r/min | 200 | 300 | ||
At 4000 r/min | 180 | 230 | |||
BXM460 | 5 | At 2~3000 r/min | 200 | 250 | 100 |
At 4000 r/min | 180 | 220 | |||
10, 15, 20 | At 2~3000 r/min | 300 | 350 | ||
At 4000 r/min | 270 | 330 | |||
30, 50, 100, 200 | At 2~3000 r/min | 450 | 550 | ||
At 4000 r/min | 420 | 500 | |||
BXM5120 | 5 | At 2~3000 r/min | 300 | 400 | 150 |
At 4000 r/min | 230 | 300 | |||
10, 15, 20 | At 2~3000 r/min | 400 | 500 | ||
At 4000 r/min | 370 | 430 | |||
30, 50, 100, 200 | At 2~3000 r/min | 500 | 650 | ||
At 4000 r/min | 450 | 550 | |||
BXM6200 BXM6400 |
5, 10, 15, 20 | At 2~3000 r/min | 550 | 800 | 200 |
At 4000 r/min | 500 | 700 | |||
30, 50 | At 2~3000 r/min | 1000 | 1250 | 300 | |
At 4000 r/min | 900 | 1100 | |||
100, 200 | At 2~3000 r/min | 1400 | 1700 | 400 | |
At 4000 r/min | 1200 | 1400 |
About Load Position

Hollow Shaft Flat Gearhead
Motor Product Name | Gear Ratio | Permissible Radial Load | Permissible Axial Load N |
||
---|---|---|---|---|---|
10 mm from the Gearhead Mounting Surface N |
20 mm from the Gearhead Mounting Surface N |
||||
BXM230 | 5, 10 | At 2~3000 r/min | 450 | 370 | 200 |
At 4000 r/min | 410 | 330 | |||
15, 20, 30, 50, 100, 200 | At 2~3000 r/min | 500 | 400 | ||
At 4000 r/min | 460 | 370 | |||
BXM460 | 5, 10 | At 2~3000 r/min | 800 | 660 | 400 |
At 4000 r/min | 730 | 600 | |||
15, 20, 30, 50, 100, 200 | At 2~3000 r/min | 1200 | 1000 | ||
At 4000 r/min | 1100 | 910 | |||
BXM5120 | 5, 10 | At 2~3000 r/min | 900 | 770 | 500 |
At 4000 r/min | 820 | 700 | |||
15, 20 | At 2~3000 r/min | 1300 | 1110 | ||
At 4000 r/min | 1200 | 1020 | |||
30, 50, 100, 200 | At 2~3000 r/min | 1500 | 1280 | ||
At 4000 r/min | 1400 | 1200 | |||
BXM6200 BXM6400 |
5*, 10 | At 2~3000 r/min | 1230 | 1070 | 800 |
At 4000 r/min | 1130 | 990 | |||
15, 20 | At 2~3000 r/min | 1680 | 1470 | ||
At 4000 r/min | 1550 | 1360 | |||
30, 50, 100 | At 2~3000 r/min | 2040 | 1780 | ||
At 4000 r/min | 1900 | 1660 |
- * 400 W type only
Rotation Direction
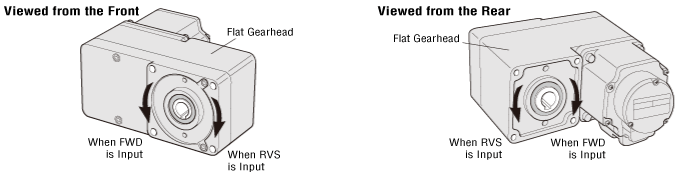
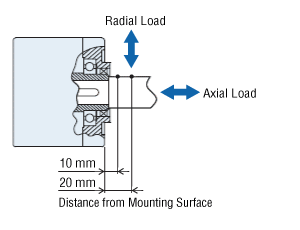
Round Shaft Type
Motor Product Name | Permissible Radial Load | Permissible Axial Load N |
|
---|---|---|---|
10 mm From the End of the Output Shaft N |
20 mm From the End of the Output Shaft N |
||
BXM230 | 87.2 | 107 | 10 |
BXM460 | 117 | 137 | 20 |
BXM5120 | 156 | 176 | 25 |
BXM6200 BXM6400 |
197 | 221 | 25 |
Vertical Operation (Gravitational operation)
BXII Series achieves stable speed control even during gravitational operation.
During vertical operation (gravitational operation), shown in the figure below, normally an external force causes the motor to rotate and function as a power generator. If this energy is applied to the driver, an error will occur.
The accessory regeneration resistor (sold separately) can convert regenerative energy into thermal energy for dissipation. Use the accessory regeneration resistor when using the motor for vertical operation or when braking a large inertial load quickly.
Regeneration Resistor Product Name | Applicable Product | Continuous Regenerative Power | Instantaneous Regenerative Power |
---|---|---|---|
EPRC-400P | BXSD30-A2, BXSD30-C2 | 100 W | 240 W |
BXSD60-A2,BXSD60-C2 | |||
BXSD120-A2,BXSD120-C2 | |||
RGB100 | BXSD200-A2,BXSD200-C2 | 100 W | 800 W |
BXSD400-A2 |
- Install the regeneration resistor in a place that has the same heat radiation capability as the heat sink (Material: aluminum 350×350 mm, 3 mm thickness).
Regenerative Power
The regenerative power can be estimated using the formula below. Use the calculated value as a reference.
Regenerative Power (W) = 0.1047 × TL [N·m] × N [r/min]
TL: Load torque N: Rotation speed
Gravitational Operation Capability
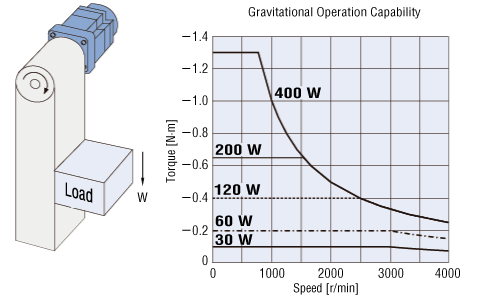
- Continuous gravitational operation exceeding the range of continuous regeneration resistor will trigger the built-in thermal protector (150°C).
- Use electromagnetic brake type for gravitational operation.
มาตรฐาน
Regulations and Standards Materials
Documents about compliance with regulations and standards can be downloaded from the "Data Download" tab on the product details page.
(The types of files available for download vary by product.)
Explanations of the Global Laws, Regulations and Standards can be found here.
Information about our compliance with safety standards for each of our product models can be found here.
Hazardous Substances
The product does not contain any substances (10 substances) exceeding the regulation values of the RoHS Directive (2011/65/EU, 2015/863/EU).
การกำหนดค่าระบบ
สายเคเบิลและอุปกรณ์เสริม
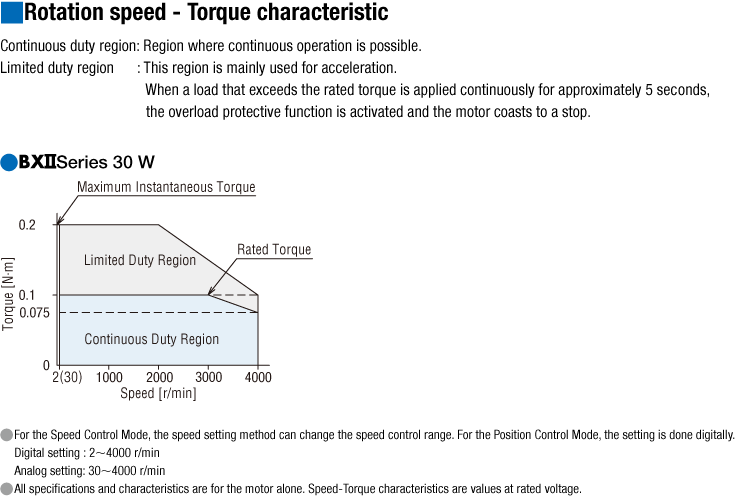
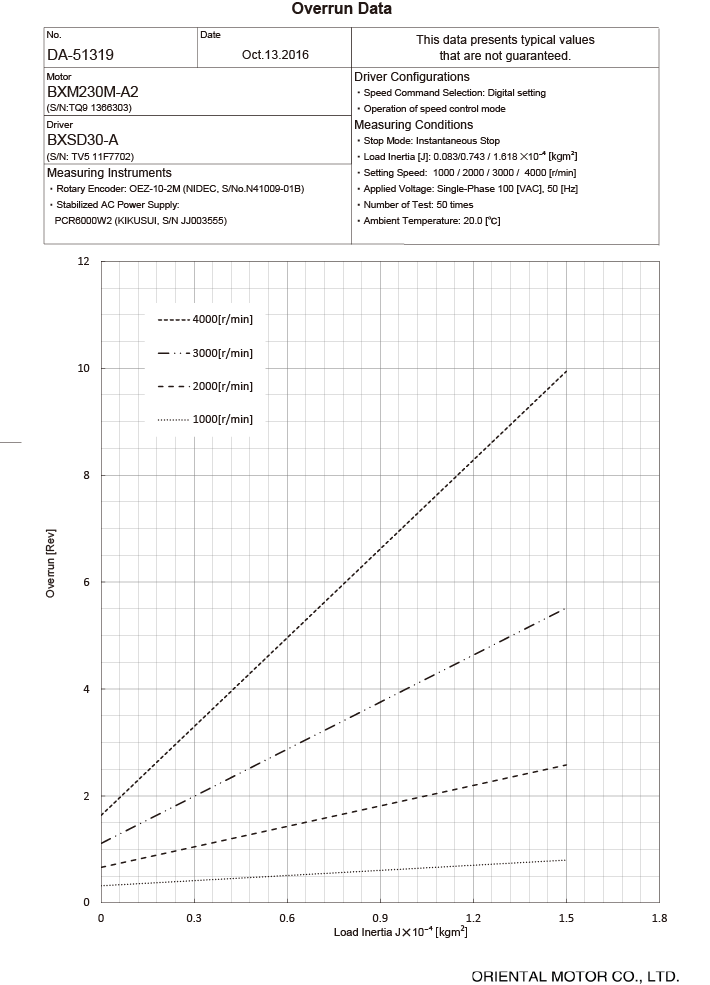


